Sponsored by:

Designing a Sustainable and Affordable Cooling Technology for Mattress
Cameron King, Dio Oey, Lakshmi Prerana Panchumarti, Elijah Tan., Thomas Thwaite, Wendi (Allen) Wu

Fatigue
Testing description
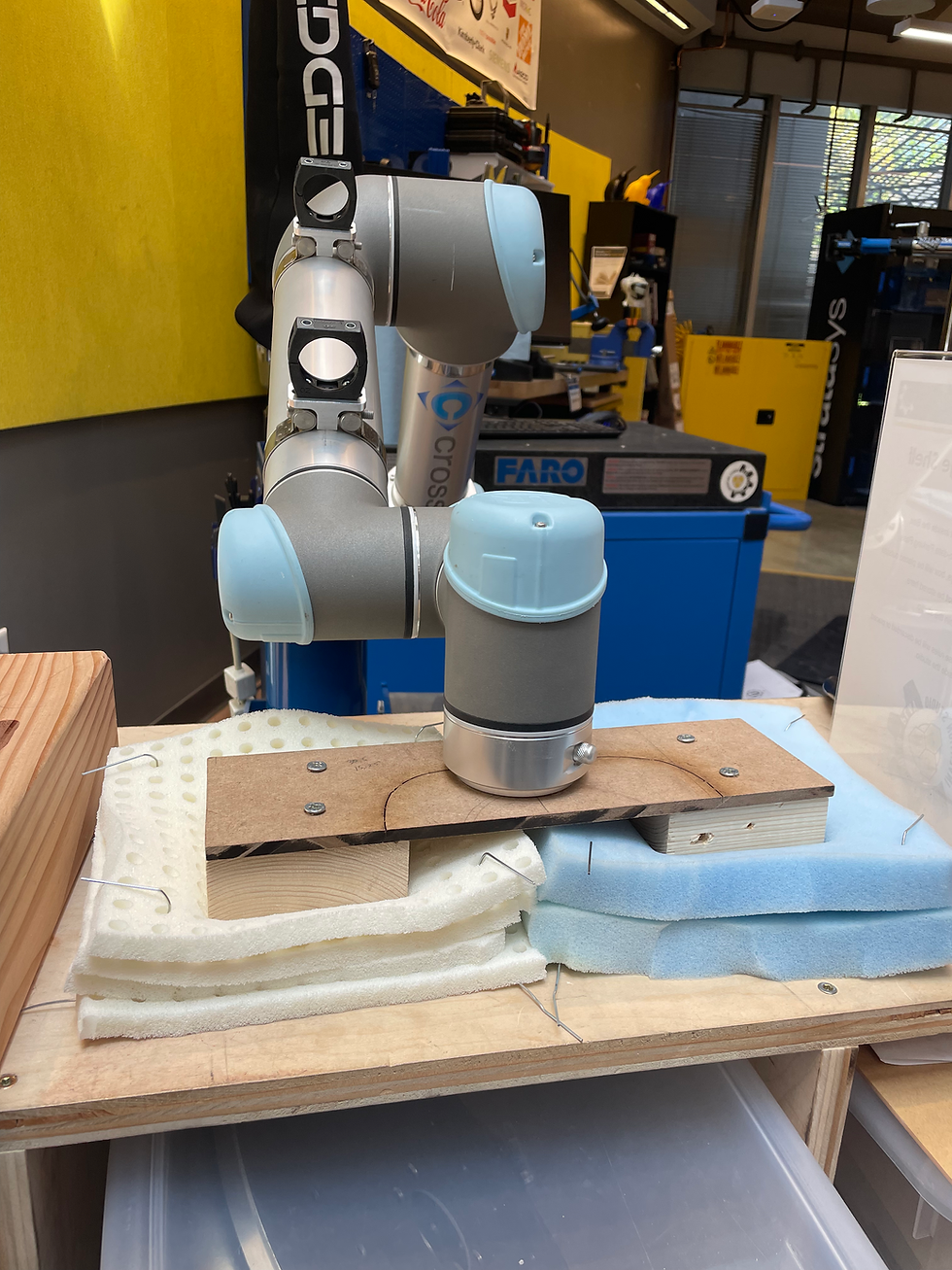

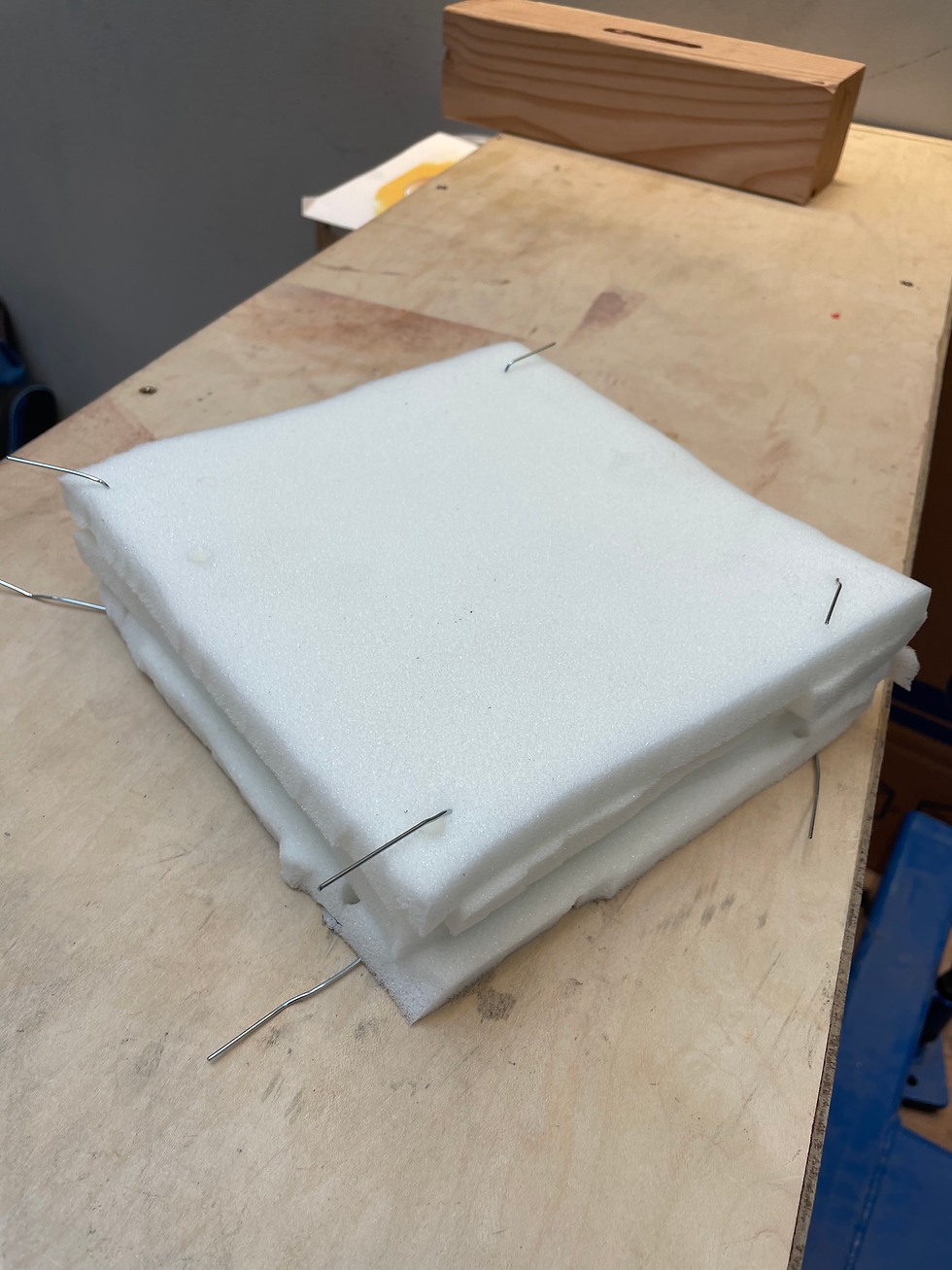
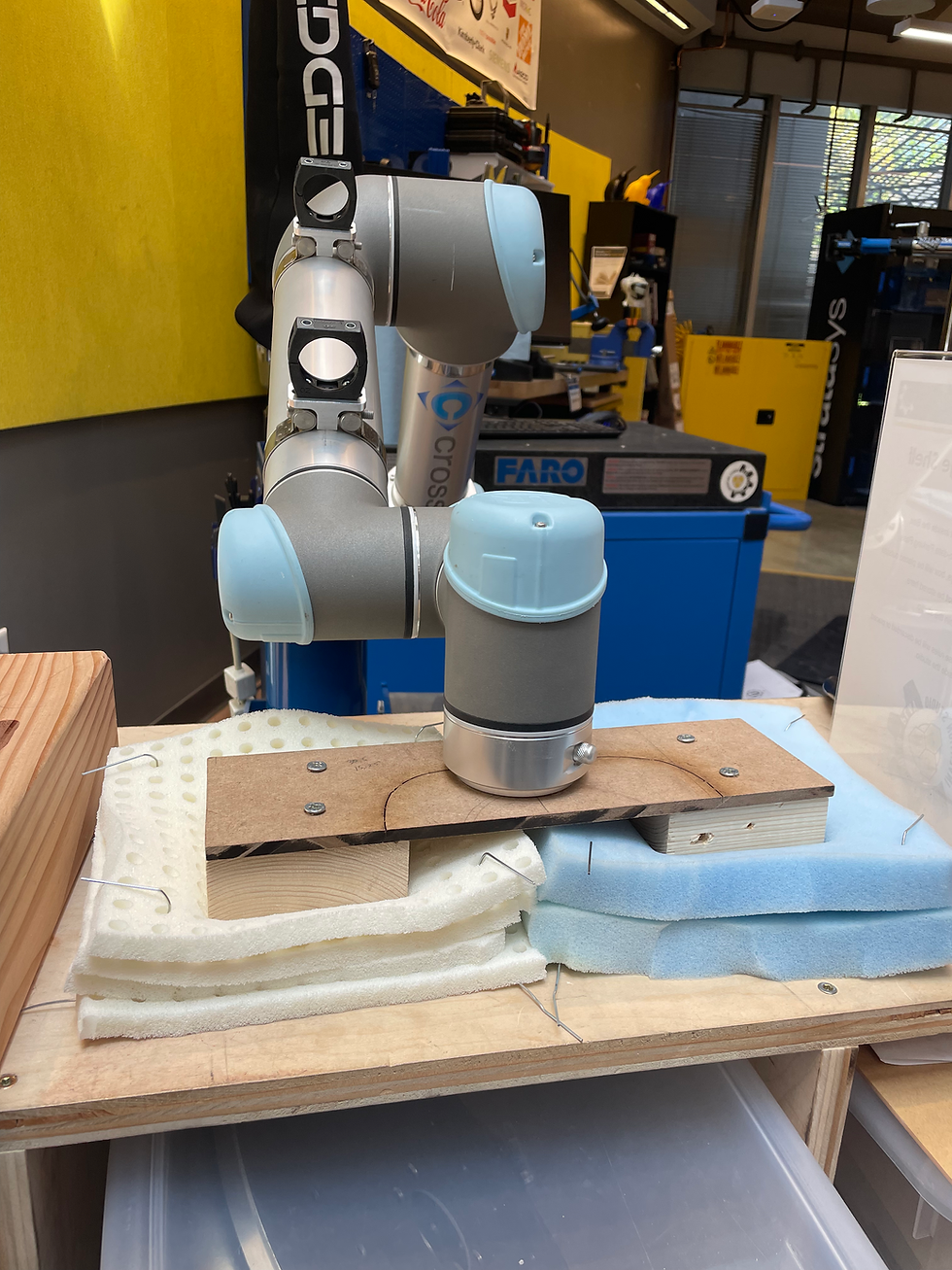
Fatigue testing is used to measure the firmness or thickness loss of a foam or mattress. Fatigue testing allows us to figure out how effective our final mattress model is in terms of thickness retention level. The industry follows an ASTM F1566 standard on the Admit H-frame mattress tester for measuring mattress fatigue and firmness retention [11]. The value of firmness retention is measured before and after the compression plate is lowered onto the surface of the mattress and run for 100,000 cycles.
However, as our mattress samples are significantly smaller than an actual mattress, a modified test method was used. A universal brand robot was used to cyclically compress the sample (Appendix E-1). The robot was programmed with a loop iteration where the robotic arm initiated on the position slightly above the matters at position waypoint1, then lower to the position wayponit2 where the compression happens, and it holds for 5 seconds (Appendix E-2). This iteration can happen 500 times which allows repeated compression motions for the robotic arm. Foams that are 8x8 inches and 2 inches thick were tested, so a modified testing method was used because it is more suitable for the smaller size. For each sample, the robotic arm pressed 1 inch down relative to the top surface of the foam and was held in the compressed position for 5 seconds, constituting one cycle. Two square woodblocks of 2.5 inches by 2.5 inches work as indenters and attach to the header of the robotic arm, so two samples could be tested simultaneously (Appendix E-1). The thickness of the foam was recorded every 500 cycles for 4000 cycles. To prevent the four corners of the foam from lifting during compression, four steel wires string up the different layers of foam (Appendix E-1). The thickness reduction of standard memory foam, cooling memory foam and ventilated latex foam were recorded and compared to the prototype's data. In industry, a mattress is considered to have failed the compression fatigue test if its thickness is reduced by more than 3%.
Result
Figure 16 shows the percent change of thickness reduction for every 500 cycles of compression until 4,000 cycles. The standard memory mattress foam, latex foam, pneumatic mattress foam and cooling mattress foam from Serta are tested as references and used to determine how well the prototype sample did on the fatigue testing. Among the four reference samples, the cooling mattress shows the greatest retention force under compression with only 1.36 percent thickness reduction. Latex and pneumatic foam show a similar result with 1.85% and 1.92% thickness reduction. The standard memory foam has a worse result compared to other samples with a 2.47% thickness reduction. The prototype holds a 1.58 percent thickness reduction which is better than all reference samples besides the cooling mattress. Even though the silicone rubber on the prototype has better resistance to force, the result doesn't exceed the cooling mattress due to half of the prototype’s layer is made of the standard mattress and one-fourth of it is made of latex foam. Overall, the thickness reduction of the prototype is less than 3 percent, and it is above the average market standard.
