Sponsored by:

Designing a Sustainable and Affordable Cooling Technology for Mattress
Cameron King, Dio Oey, Lakshmi Prerana Panchumarti, Elijah Tan., Thomas Thwaite, Wendi (Allen) Wu
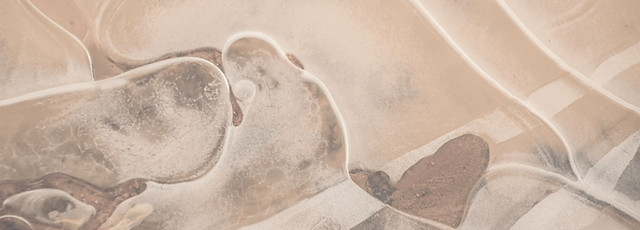
Moisture and Wicking Testing
Testing description
Moisture management is important for the consumer as sweating causes discomfort to the sleeper. Fabric layers used in mattresses are the first design element that can be altered to promote moisture control. Water retention is the percent moisture retention of the specimen after being submerged in deionized water and hung vertically. Moisture wicking refers to the movement of liquid by capillary action along or through a material. Vertical moisture wicking was used in this test specifically.
We tested the moisture and wicking abilities of the Tencel fabric versus a standard rayon fabric for the mattress topper. The AATCC standards AATCC TM197-2011e2(2018)e and AATCC TM199-2013e(2018)e were used to test for vertical wicking, moisture retention, and drying time. The endpoint parameter used for the moisture analyzer was A60 and the temperature set was 105°C. Specific water quantities, 5 mL and 7 mL, were added to Tencel and rayon respectively, Additionally, we did not have access to a vertical drying stand so a peg drying stand with binder clips on the end were used to hang the samples as part of the moisture retention test for TM199-2013. For the water application, the specific precision water application tool was not available, so the amount of water was measured out and applied to water as uniformly as possible. A wire support rack was not made available, so to substitute two sample pans were punctured with holes to simulate as closely to a support wire rack as possible. Test procedures that changed for the vertical wicking test include the use of an elongated pan as one was not able to be procured so a 32 oz. plastic container was used to conduct the test.
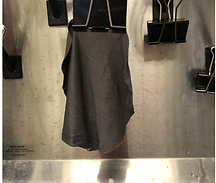
D-1: How the drying was done for the moisture retention test as a vertical drying stand was not available. The sample was clipped as close to the edge.

D-2. Figures above show the state of the moisture analyzer in the opened and closed state. The substitute wire support rack is also shown
D-3. Figure showing the set up for the vertical wicking test since an elongated sample pan was not available.

Result

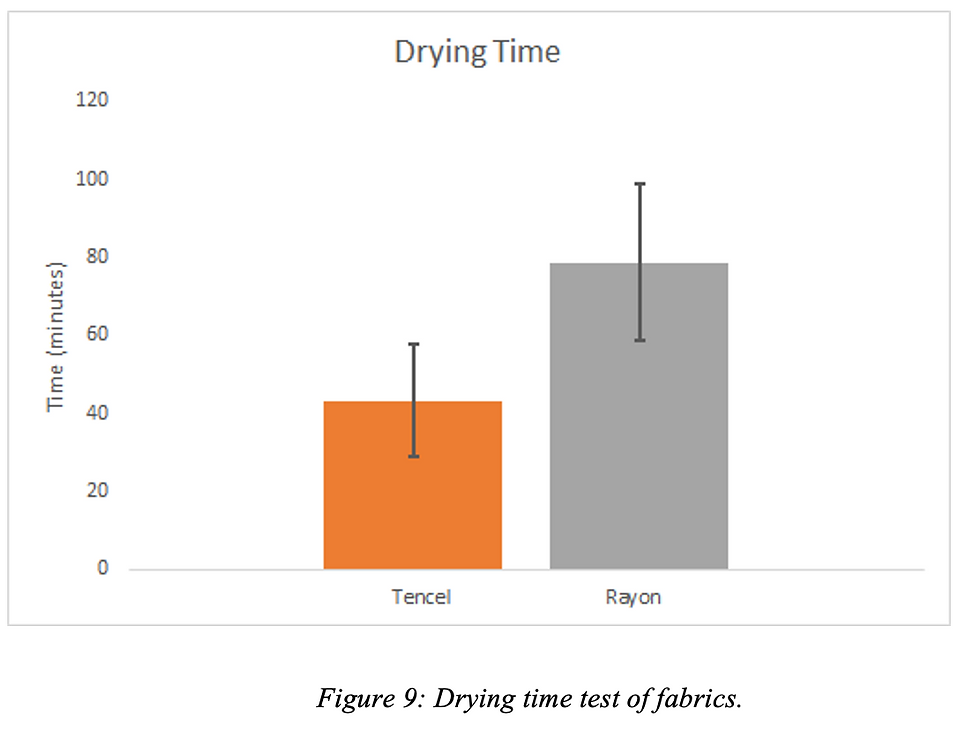
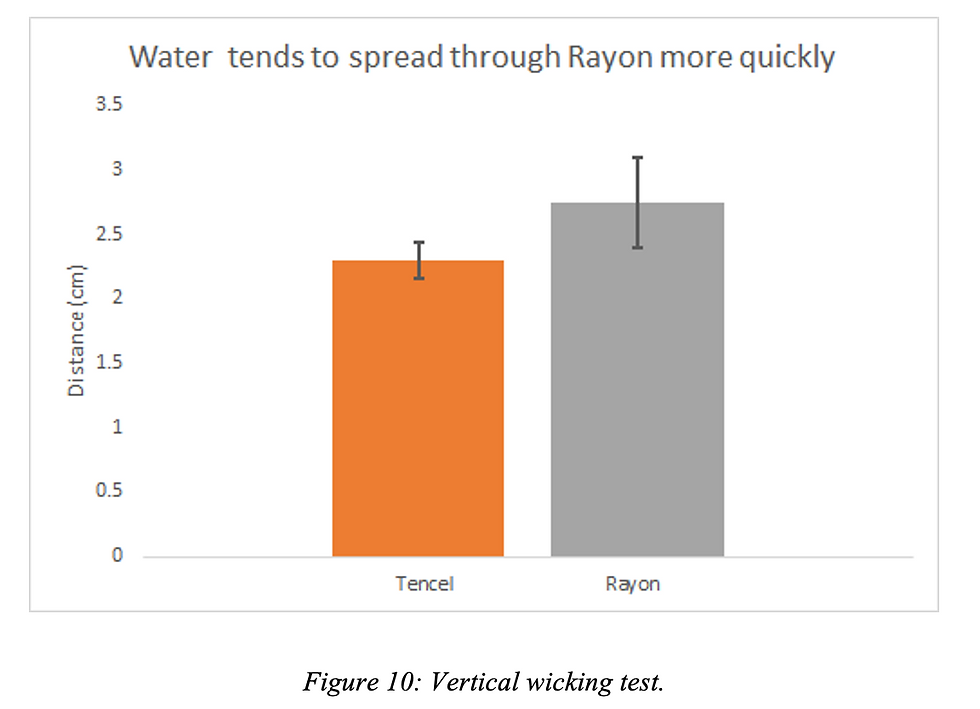


To determine if Tencel fabric would perform better as the fabric layer than the traditional rayon blend, drying time testing and moisture retention testing was done to determine the amount of water to be added according to AATC TM199. This test gives an initial picture of how the two materials will perform in the later test. From Figure 8, we can infer that since there was a lower percentage of moisture remaining in the Tencel sample that the material has better wicking properties than the rayon blend.
The results of the drying time test can be seen Figure 9, showing that the Tencel samples dried much more quickly than the rayon blend. The results showed no overlapping in the standard deviation, although there was an outlier in the rayon data. The outlier had a drying time of 144 minutes (about 2 and a half hours) and at first it was believed that the cause could have been from humidity; however, the humidity of the day was within the tolerance range. Other samples tested that were not within the humidity range still performed within the expected drying time ranges. This may be due to the OHAUS moisture analyzer being able to reduce humidity or other outside factors as the testing platform inside of it closes itself off from the room. Since humidity was no longer the expected reason of the outlier, we suspect that the uniformity of the water application was not met and perhaps this made it more difficult to dry the oversaturated regions and lead to the outlier.
In the vertical wicking test, the rayon performed unexpectedly well and outperformed the Tencel samples (Figure 10). However, the error bars and standard deviations overlap, indicating that definitive claims cannot be made. The results in Figure 10 could be explained with a few different possible mechanisms. The rayon may have shown a greater wicking distance due to the difference in wicking mechanisms, or a lower fiber thickness compared to Tencel. There may also have been processing differences between the products, and the rayon looks to be a spun yarn while the Tencel yarn is a continuous straight yarn. Another reason could be due to the Tencel’s structure of nanofibrils and how they direct the moisture to the fiber core instead of using capillary action. Due to these reasons using the vertical wicking test was not an accurate choice for the comparison of wicking between these two materials.
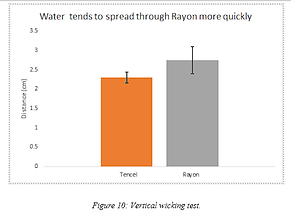